19.08.14 , ,
When choosing grounding made of steel rods, the following question arises: which coating (copper or zinc) shall we choose for the rods? If the steel core of the rod provides strength and setting the electrode deeper, then what can the coating material influence?
In this respect, one should turn to the basics of chemistry. In the reaction between zinc and steel, steel is an oxidizing agent, while zinc is a reducing agent. Thus, first of all, zinc is oxidized protecting steel. When all its mass has taken part in the reaction, i.e. it has oxidized, steel will begin to corrode.
In the reaction between copper and steel, copper is an oxidizing agent, while steel is a reducing agent. In this case, iron is oxidized in the first place, copper is thereby protected. Here, we should pay attention to the peculiarity of the electrochemical reaction: it is possible only in the presence of an electrolyte / water. If the steel is isolated from it, the oxidation reaction stops.
Thus, the copper coating must have a thickness that allows the rod set to a greater depth without stripping the rod core. The ideal thickness of the copper layer is 250 microns (based on the research data). [[placeholder]]This value characterizes the mechanical resistance of the coating, as setting the rod into the ground, the possibility of "meeting" stones will not damage the coating seriously.
With zinc coating, it is not necessary to mechanically protect the coating during assembly. Damage to the coating integrity does not result in any consequences, as zinc protects the iron anyway. However, due to the small thickness of the zinc coating, the service life of such rod is reduced to 15-25 years. Besides, metal structures adjacent to it reduce the service life of a zinc'coated rod.
99-micron thick zinc-coated ground rod extracted from the soil (clay loam) 10 years later
The thickness of this rod copper coating ranges between 200 micron and up, which increases the service life of the copper-coated rod up to 30 years in aggressive soil and up to 100 years in regular loam. There is no point in ignoring the issue of cash expenses, as in order to achieve a long service life of the zinc-coated rods, it is required to increase the coating thickness, which will increase the product price manifold, while the copper-coated rods are affordable.
254-micron copper-coated grounding rod extracted from soil (loam) 10 years later
As it can be seen from the comparison above, the advantage of copper coating is obvious. Having chosen copper-coated grounding rod, you will receive a reliable grounding device, which will last for a very long time.
Related Links:
Related Articles:
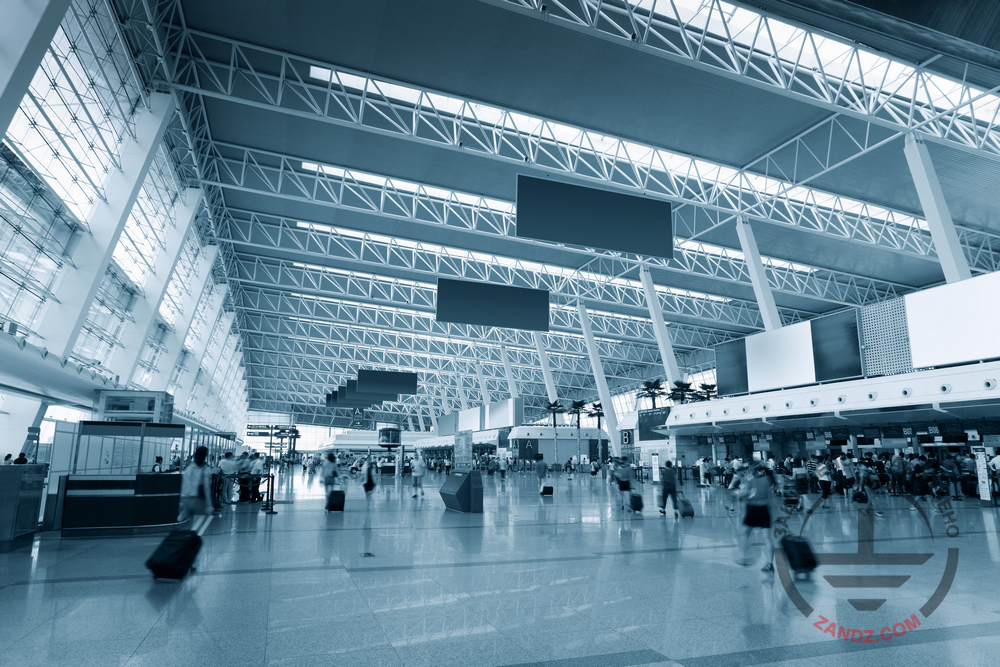
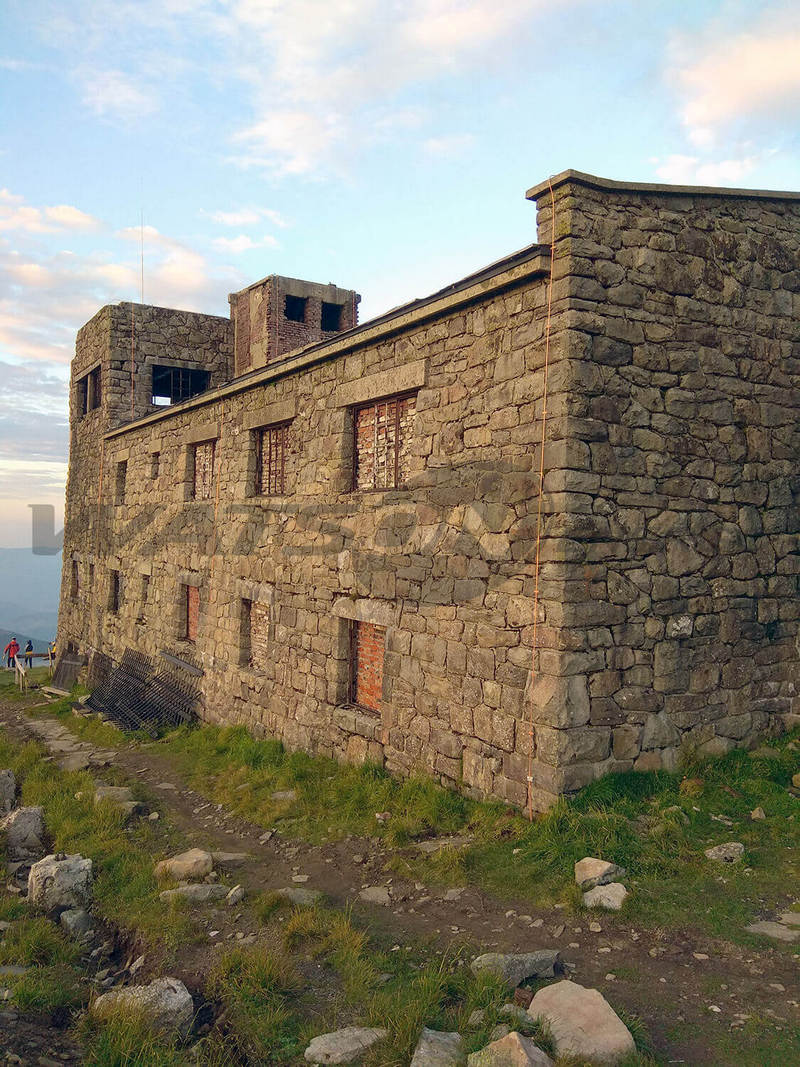
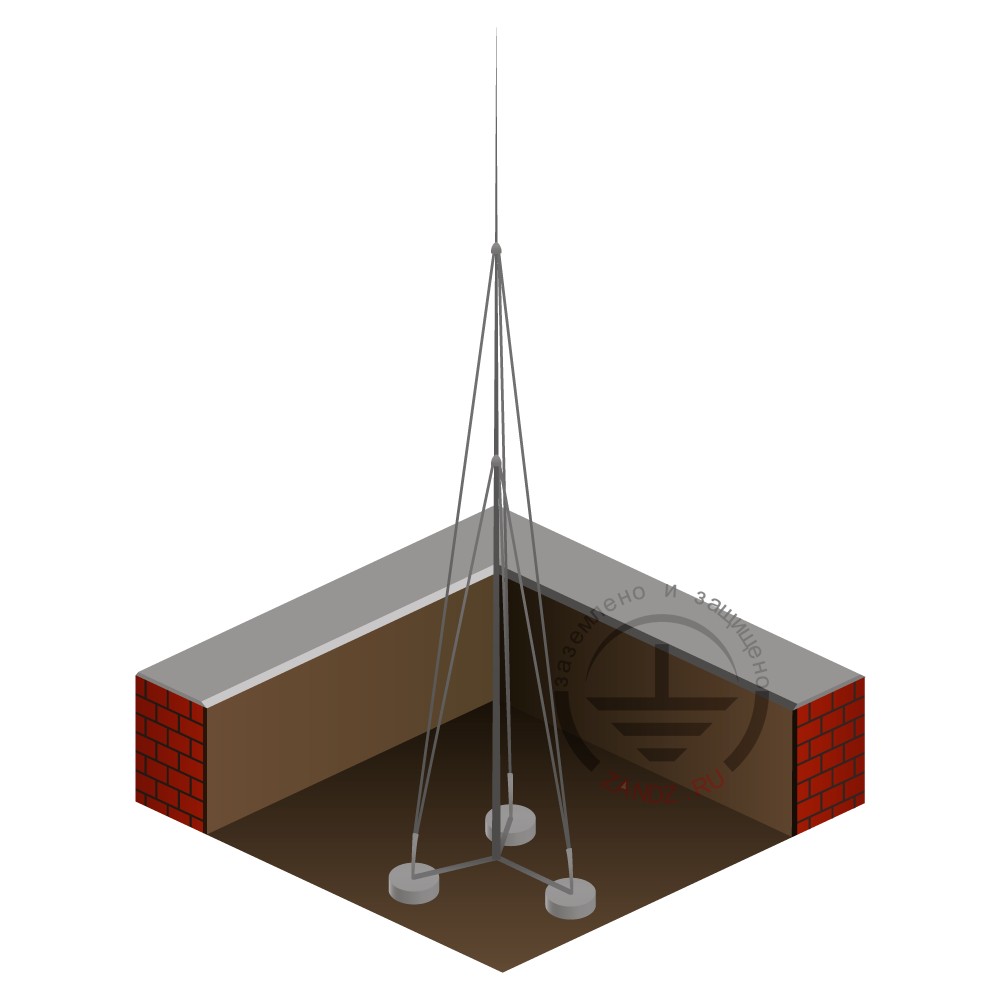
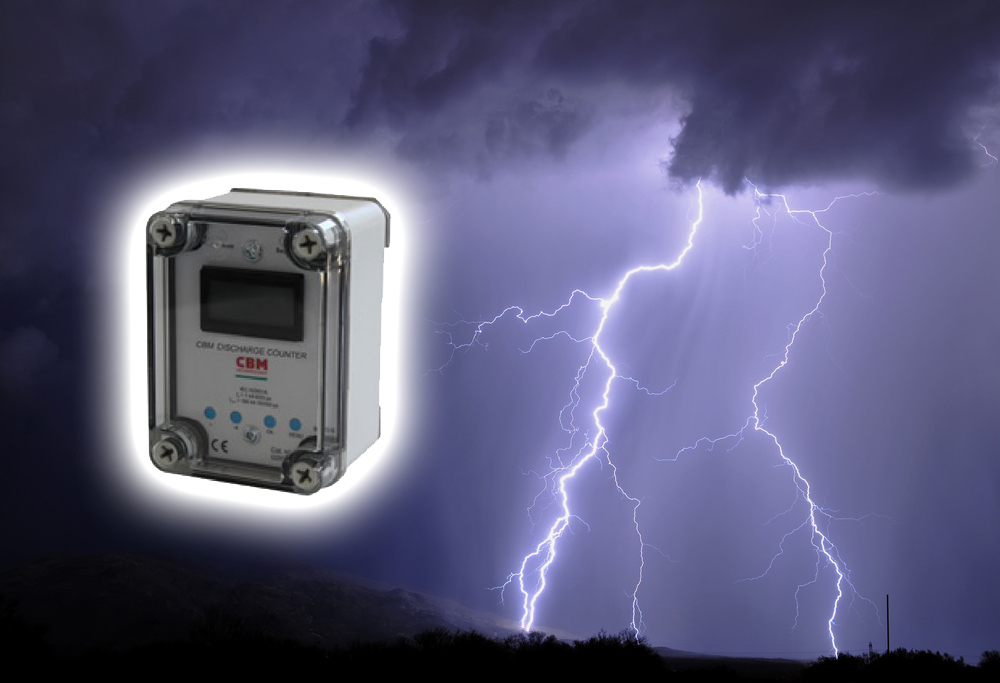