Welding is a method of creating a permanent connection of various products, parts, stucture components. Welding is performed by the following processes:
- at local or general heating of parts;
- under the influence of plastic deformation;
- when heating and deformation are combined.
Welding is carried out by the emergence of atomic bonds at the junction. The strength of welding connection is provided by the formation of interatomic bonds between the elementary particles of welded parts, which means that you need to provide their maximum approach and contact. The majority of metals used under normal conditions are solid crystalline substances. Thus, in order to carry out welding it is necessary to bring a large number of atoms of solid parts together to a minimum distance. But the thing is that metals have a crystal lattice. Its peculiarity - tight retention of substance atoms in the nodes. This phenomenon gives the metal its high strength properties. One way of weakening of metal lattice rigidity and increasing the mobility of atoms is increase of temperature. The higher is the heating temperature, the less is the retention of atoms in lattice nodes. When the temperature of metal reaches the melting temperature, it becomes liquid, and the atoms gain high mobility. Therefore, to connect the parts it is necessary to ensure melting of a small portion of metal in the welding area. Melting, liquid metal forms a weld pool. In the process of cooling the metal hardens, thereby providing a firm conjunction.
According to GOST 19521-74 welding is subdivided into three classes according to the type of energy used in the process of connection:
- Thermal
- Thermomechanical
- Mechanical
Welding Classes: thermal, thermomechanical and mechanical
The process of mechanical welding
During welding, the following problems may appear:
- formation of such defects as cracks;
- occurrence of material deformation;
- reduction of mechanical, electrical characteristics of the material in the welding area.
Such kind of welding as exothermic welding is devoid of these disadvantages. This kind belongs to the thermal class. The thermal class includes types of welding carried out by the use of thermal energy. Exothermic welding presents itself a welding process which is carried out by filling a gap between the joined products, pre-heated to 400-7000C with liquid metal. Such liquid metal is recieved by thermite burning. That is why, such a welding is called thermite.
Thermite is a friable mixture of magnesium and aluminum with oxides of different metals. At the ignition, a mixture intensively burns with the release of large amounts of heat. Copper-aluminum and iron-thermite aluminum thermite play especially important role for welding of conductive elements. They include coarse (up to 1mm) powdered metal aluminum and iron oxide or copper oxide. In a mixture, aluminum plays the role of a burnable metal, since it has a great heat of oxide formation. Iron or copper oxides have low heat of formation, that is why they become oxygen donors in the reaction.
The mixture must be heated to at least 10000C in order to react. In the result the termite begins to burn intensely throughout. The process is described by the reactions:
- 3Fe2О4 + 8Al = 4Al2О3+6Fe (if the mixture includes iron oxide);
- 2Аl + 3СuO = Al2O3 + 3Cu (if the mixture includes copper oxide).
Reaction time - not more than 20 seconds. It may vary depending on the degree of components grinding, that is, the smaller the grains are, the faster the termite will burn. In the result of burning of 100 grams of thermite mixture, about 310 kJ of heat is produced. It is a relatively small figure (for example, burning of 100 grams of carbon fuel produces up to 3 ∙ 103 kJ of heat). However during burning the thermite gains quite a high temperature - about 30000C. This happens due to the fact that the thermite burns only with the participation of the components included in its composition, it means that 100 grams of termite forms 100 g of the exothermic reaction products. While burning, solid fuel takes oxygen from the air, which greatly increases the weight amount of reaction product in comparison to the mass of the intact substance.
In case of copper-aluminum thermite, aluminum and copper oxide are the reaction products. Melting points of these substances are 20720C and 10850C, respectively. Consequently, both reaction products are formed in an overheated liquid state. As a rule, burning of a thermite mixture is carried out on special fire-proof crucibles. This way, the obtained liquid substances are decomposed to layers: top layer - alumina (slag) and bottom layer - metallic copper. As a rule, beside copper and aluminium oxide, the composition of exothermic welding contains diverse additives. Their functions - improvement of strength properties of thermite metal (copper), increase of its output, and reduction of reaction temperature. Ferroalloys are usually used as additives favorably influencing properties of thermite mixture. For example, the composition of copper thermite mixture includes ferromanganese. Changing the concentration of additives, it is possible to influence the composition and properties of the metal copper.
There are several ways of carrying out exothermic welding:
- pressure welding;
- fusion welding;
- Combined welding.
In the first case, thermite mixture is only used for heating of the conjoined parts. Conjunction is made directly with the press, which is installed prior to the process of details' conjunction. After completion of welding of products, frozen products of the reaction are removed. In the second case, liquid copper resulting from thermite burning comes in contact with the welded metal products. The latter method combines two, described above. The second method is more widely used in electrical engineering. Using copper-aluminum termite, it is possible to weld not only copper conductors, but also products of galvanized, stainless, unalloyed and other steels. Presence of copper oxide in the thermite mixture is very advantageous for several reasons:
- high electrical conductivity obtained in the process of reaction of pure copper and low resistivity;
- high corrosion resistance of copper;
- good copper adhesion to different metals.
At the present day, various welded construction and installations are used to carry out thermite welding. However, the principles of their operation and exploitation are similar and resolve themselves to a few simple operations. A special form of graphite performs the role of fire-proof crucible. Welded conductors are placed into it. Then thermite mixture is put in the form. The used mixture can be placed in a special package in the form of powder, or be pressed and formed in the form of temperature-indicating crayon or rods. Electric discharge or auxiliary ignition mixture capable to ignite from a match is used for the ignition of thermite. Welding installations are equipped with special control units. The thermite mixture burns in such a construction due to the emergence of sequence of discharges charges. After ignition it is necessary to wait for the cooling of the welded joint. The process takes about two minutes. An example of a welded structure is shown on Picture 1.
Examples of welded structures
The use of exothermic welding to connect conductors is very effective for a number of reasons:
- good conductive properties of copper (in case of copper thermite);
- connectivity of conductors made of different materials;
- thanks to strong interatomic bonds appearing in the result of welding, there is no deterioration of conductors's characteristics;
- possibility of using welded conductors in various environments due to high corrosion resistance;
- installation does not depend on external energy sources;
- resistance to repeated short-circuit currents;
- rapidity of execution of the present type connection;
- performance of a welded joint does not require special skills;
- ultimate load on the connection current is not lower than the ultimate load of connected elements.
See also:
- More details about exothermic welding
- Copper-plated steel test
- Grounding. What is it and how to make it.
- Types of air terminals: mast, cable wire and mesh cage
- Surge protection
Related Articles:
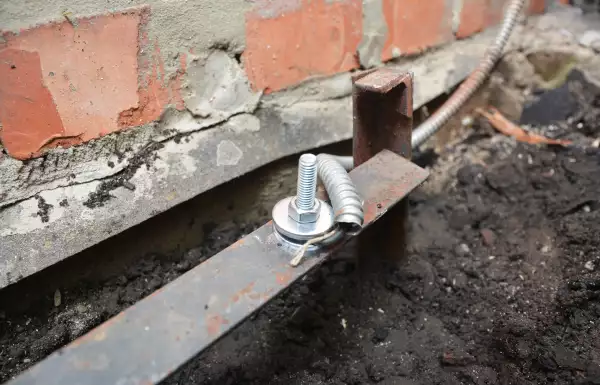
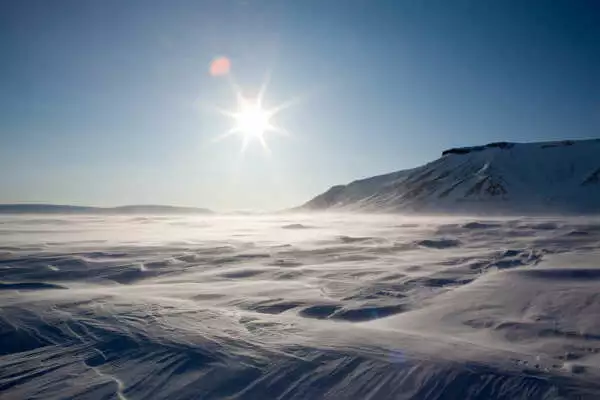
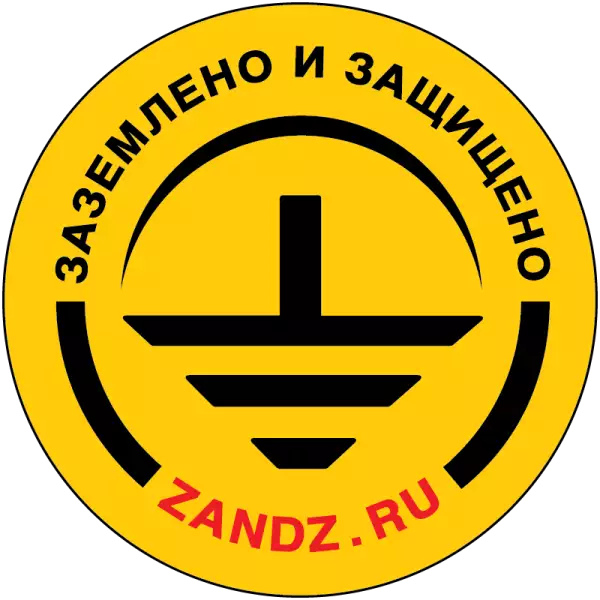
