15.10.14 , ,
In March 2014 our staff visited the GALMAR plant where he made sure of the highest quality of products used for ZANDZ grounding kits. We present you an interesting report!
GALMAR office and plant are located in western Poland, in Poznan.
Equipment for the manufacture of GALMAR products, as well as auxiliary facilities: a warehouse of ready products and transformer substation are housed in several buildings outside Poznan.
Copper bonded ground pins
A circle of steel, having the necessary characteristics (grade) is used for the manufacture of copper-bonded pins. The most important characteristic for a base of a grounding pin is a tensile strength which should not be less than 600 N / mm2. This option is clearly standardized by the international standard IEC 62561-2: 2012 and the Russian standard on its base GOST R IEC 62561.2-2014.
The roll stock comes to the manufacture in the form of coils, after what it goes through machine processing.
After the machine processing, the rough material goes to the reagent baths, where it goes through many different electrochemical reactions, including electrolytic copper plating.
After trimming the technological edges, the ends of the pins are grinded:
Then the almost ready pins are threaded and we get a brand new ground pin!
Ready copper-bonded pins are packed and sent to the warehouse of finished products:
During the production there happens a random selection of a coppered pin for regular testing for the compliance with the required specifications.
First of all, it is thickness of the copper plating, which should not be less than 250 microns, which is clearly governed by the same standards as the mechanical properties of steel - the international standard IEC 62561-2: 2012 and the Russian analogue - GOST R IEC 62561.2-2014.
Further tests on the coating plasticity and adhesion are carried out (more details on a separate page of the site).
Also the special stand checks the tensile strength.
This sample had a tensile strength 701 N/mm2 (the measuring stand fixed the strength at break - 111 kN).
There is a "museum" of coppered ground pins at the GALMAR plant, where the owner has been collecting samples of products from different industries,holding some comparative tests for the second decade.
According to his words, the main problem in the market is associated with poor-quality products, which is mispresented by unscrupulous manufacturers and sellers as high-quality: distortion of information about product parameters, deception and active exploitation of customers' ignorance about the existing standards. In particular, ignorance exploitation about the usual for this product standard IEC 62561-2: 2012 (Russian GOST R IEC 62561.2-2014).
The use of low-quality products at the sites is fraught with the following consequences:
- Steel having insufficient tensile strength, bends easily and poorly transmits the impact impulse from the electric breaker hammer during installation.
- Copper layer of minor thickness on the ground pins (many manufacturers are only making 100 microns) is easily scartched during plunging into the ground and is damaged at the thread during assembly due to load impact during burial. After installation into the ground in places of baring steel base, there appear points of very strong galvanic corrosion on pins that destroy the steel throughout the depth in 1-2 years.
- Special danger is that the copper foil of the former protective coating continues to hold not strong electrical currents and the measurement of the damaged grounding devices show normal results. However, when passing surge currents (lightning or accident in electrical equipment/ power line) this foil instantly evaporates, "disabling" ground electrodes in hundredths of seconds and leaving the facility without any grounding at all.
Copper bonded steel tape
Manufacture of copper bonded tape is not very different from the above-described algorithm. Rolled steel of the required quality comes in the form of coils. After the machine processing, the tape passes through the line of continuous copper plating and is formed into coils of the length required for the customer (eg, into coils of 10, 20 and 50 meters for the import into the Customs Union countries via IMAG company). GALMAR refused from the production of copper-bonded conductors in the form of whips, because whips are very uncomfortable during transportation and installation at customer sites.
After the excursion to the production, Professor Marek Loboda, invited from the Warsaw University of Technology held a training in which he spoke about the current EC standards regarding grounding and lightning protection.
On the left - Mr. Robert Marciniak, director of CBM technology (GALMARtm). on the right - Professor Marek Loboda (Warsaw University of Technology).
Don't miss!
a series of webinars will begin in late 2014 with the participation of prof. Marek Loboda dedicated to IEC 62305 (structure, function, purpose) for design engineers and other professionals. Details of the webinars will be posted on our website later.
See also:
Related Articles:
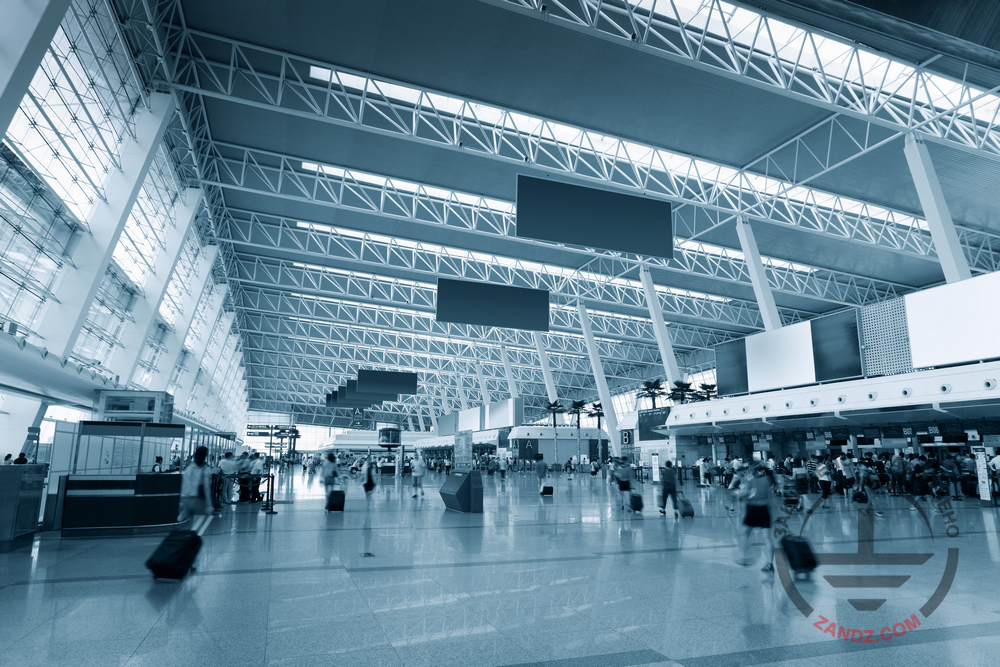
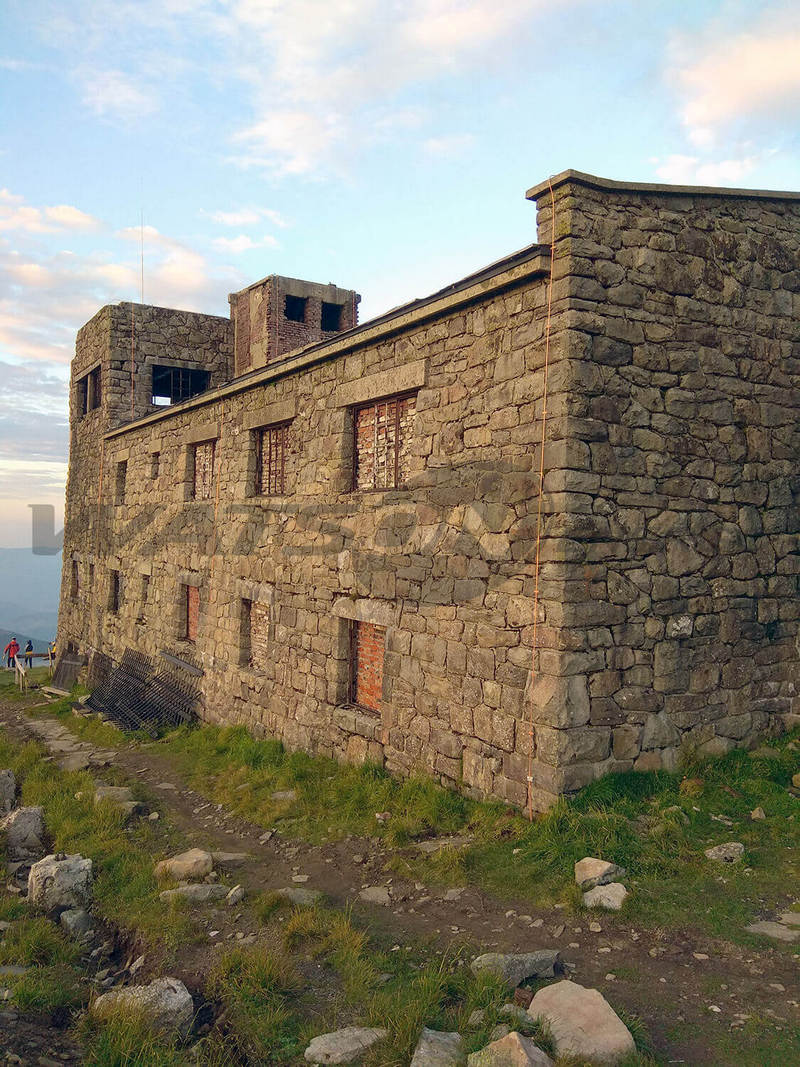
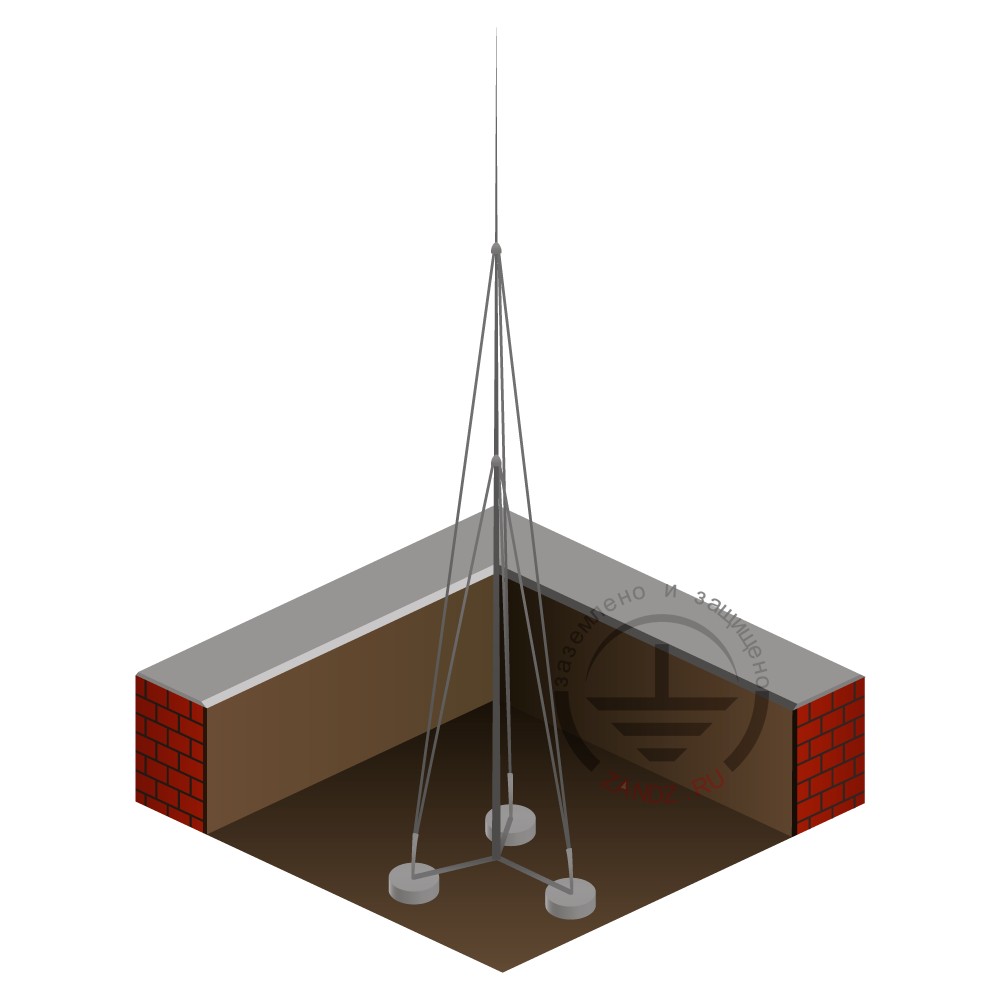
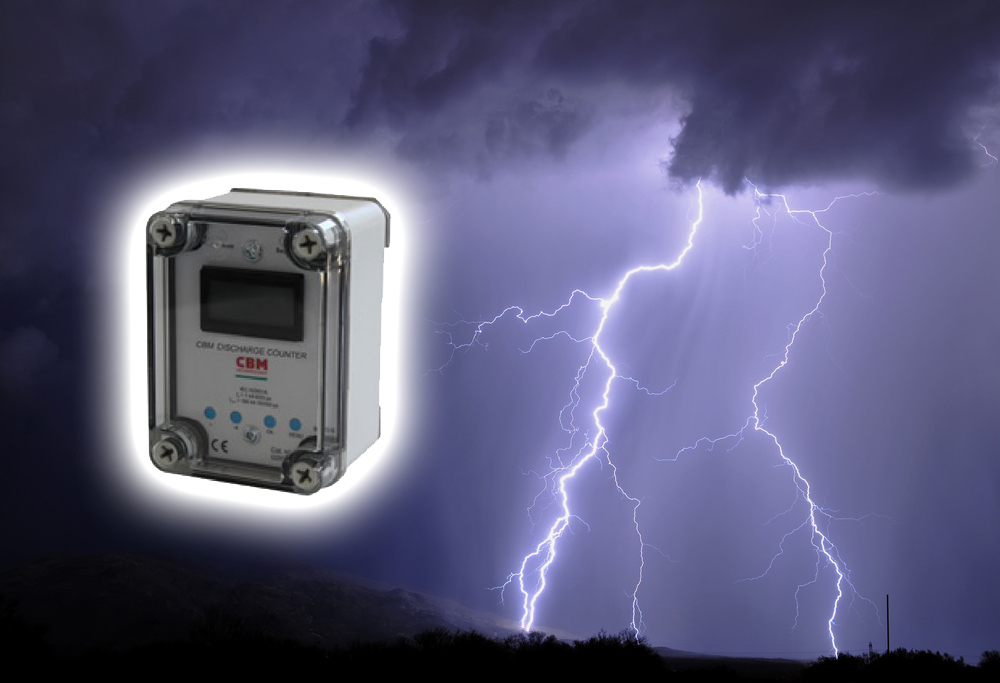