The lightning strike is considered one of the most dangerous natural phenomena, a destructive force that cannot be underestimated. A direct lightning strike into an object leads to its mechanical failure, fire, explosion, and electric shock to people and animals. The secondary lightning hazard includes powerful electromagnetic pulses that cause the failure of internal systems and damage various electric equipment.
The need for the lightning protection of objects is determined by attributing them to the categories in accordance with the RD 34.21.122-87 "Instructions for the lightning protection of buildings and structures" (hereinafter RD) and SO 153-34.21.122-2003 "Instructions for the lightning protection of buildings, structures and industrial communications"(hereinafter SO). Single-family houses belong to the third category of structures according to the RD Instructions, and to the "usual" category according to SO. This means that, unfortunately, regulations do not require the mandatory installation of lightning protection for these types of structures. The need for the installation of a lightning protection system is determined by the owner of the house on his or her own, based on the probability of a lightning strike and possible damage to the property.
Wooden houses, due to their inflammability, are a source of higher risk. Therefore, lightning protection is especially important for them and should be carried out in a mandatory manner. To effectively protect the house from possible damage, it is necessary to apply the comprehensive measures of lightning protection.
External lightning protection of wooden buildings
If the installation of a lightning protection system for a single-family house made of noncombustible materials is quite a clear task, the lightning protection of wooden building has a number of distinctive features. Let's start with the fact that any external lightning protection system consists of three main elements: air terminal, down conductor and grounding. Let us consider each of them separately.
Air terminal
Air terminal is a device designed to intercept the lightning strike. Depending on the type of air terminal, the external lightning protection system can be active (in the form of ESE lightning rod) or passive (lightning rod, catenary wire or mesh cage). For single-family houses, lightning protection is often mounted on the building itself and provides protection within a limited area. For the elements of building and parts of its roofs beyond these limits, additional air terminals are installed. According to paragraph 3.2.1 of CO2 metal roofing, connected to grounding, can itself serve as the air terminal, subject to certain conditions:
- If you want to prevent the roof from damage or burn-through, then the thickness of metal roofing should at least 4 mm for steel, 5 mm for copper and 7 mm for aluminum;
- the thickness of metal used should be at least 0.5 mm if it is not necessary to provide the protection of roof from damage and there is no danger of combustible materials inflammation under the roofing.
External metal ladders, drains, etc. can serve as down conductors in such cases.
Metal tile widely used today has the thickness of less than 0.5 mm, so roofs made of this material can not serve as an air terminal under any circumstances.
The metal of seam roofing meets the condition of being at least 0.5 mm, thick, but it is mounted directly on a flammable backing material (wooden rafters, lathing, etc.). In the case of a direct lightning strike, it is heated to a temperature sufficient to ignite, wich often causes a local fire.
It turns out that metal roofing can be considered a part of the lightning protection system only if it is laid on a non-combustible backing material, and all conductive elements are reliably connected to ensure a solid electrical linkage between them. Burn-throughs and melting can also be avoided if sheets of steel, copper or aluminum with a minimum thickness of 4 mm, 5 mm and 7 mm respectively are used for roofing.
Simple air terminals in the form of lightning rods with a length of 0.2 to 1.5 meters are widely used for houses with a metal roof. The rod is placed vertically at the highest point of the building - on the ridge of the roof. It is also possible to attach the lightning rod to the chimney after the consideration of wind loads.
The rod is made of a metal resistant to corrosion, i.e. copper, stainless steel or galvanized aluminum, observing the following requirements: cross-sectional area at least 50 sq mm, and the diameter at least 8 mm. If a hollow tube is used as the lightning rod, then it should have a tip.
The lightning protection of wooden buildings with a simple gable roof is ensured using a catenary wire, i.e. a cable stretched between two supports. The wire itself is usually made of galvanized steel with a section of 35 mm and more. It is also possible to use a copper wire.
The supports can be made of wood or steel and should withstand the tension of the wire at wind loads, as well as the load of snow or ice. The wire is attached to the supports with tension clamps and connected to down conductors.
Lightning rods a placed is such a way that the area of protection created by them covers all parts of the wooden house, including the protruding elements and structures: the edges of the structure, ridges, corners, vents and gutters, fireplaces etc. Using a mesh cage to protect the metal roofing is highly ineffective due to the fact that a lightning simply "won't notice" it. However, this type of air terminal is perfect for the lightning protection of wooden houses with non-metallic roofing, especially in case if a flat tiled roof is used, when it is necessary to protect one building that dominates over all the neighboring buildings. A mesh cage is often mounted on the roof at the construction stage. The lightning protection mesh cage is a metal wire with a diameter of 8 mm laid along the roof perimeter, and the space inside the perimeter is divided into cells maximum 6x6 meters. The wire is welded at the point of intersection. The resulting structure is connected to the ground loop using several down conductors.
Parts of the building that rise above the mesh cage, for example, chimneys or antennas, are protected by lightning rods. They are installed on special bases with consideration of the allowable distance to the roof. These additional lightning rods are included into the common system of closed loops with the mesh cage.
There is no principal difference in the protective effect of these air terminals. However, when choosing the method of external lightning protection for a house, one should consider the structure of the protected building, as well as the type of roof and roofing materials in use. Compliance with the rules and guidelines for the installation of each type of air terminal is equally important. Catenary wire lightning protection is considered the most secure while creating greater protection zone, including the area of the roof and the elements of building that rise above it. And mesh cage lightning protection does not mar up the house.
One of the options to provide the lightning protection of a wooden house is installing a lightning rod at a distance from it. A metal rod is fixed on the top of a nearby tree, that rises above the roof of the house. The rod should rise half a meter or more above the crown.Such a lightning protection system will protect the house from a direct lightning strike and, at the same time, eliminate the cause of the dangerous surge inside, as well as the burn-up of the tree itself.
If it is impossible to set the receiving device in isolation, then the catenary wire will be an effective option to protect the wooden building, provided that the distance between the air terminal and the roof is at least 0.5 m. Additionally, you need to insulate the steel support rods in their point of attachment to the roof, by installing a wooden base with the same minimum height.
Down conductor
Down conductors are designed to drain the lightning current to the grounding system. They are usually connected to the air terminal by welding or bolted clamps to ensure a strong metal bonding in all weather conditions: strong winds or a falling snow formation. The required area of contact in the case of welded connection is at least twice the cross-sectional area of the parts.
Experts recommend using copper-bonded round steel wire with a diameter of 8 mm as a down conductor. It is laid on the outer wall of the house at the greatest possible distance from doors and windows. A blank wall located in front of the wall with the front door is an ideal installation place. At least two down conductors shall be laid from each lightning rod. According to standards, down conductors are made as short as possible, without sharp bends or right angles, to avoid the risk of a short circuit. Arrange them evenly around the perimeter of the building to be protected at a distance of 25 m from each other and as close as possible to the corners, the edges of the gables, dormers or sharp protrusions, i.e. high-risk places. The recommended distance to the metallic elements of the building is 30 cm.
To prevent the inflammation of wooden house walls in case if down conductor's temperature increases during the lightning current drainage, the installation should be done at a distance of more than 0.1 meters from the facility to be protected; a metal clamp designed to attach the down conductor can be in contact with the wall. The contact of metal brackets and special bolted clamps with the wall is allowed. Do not lay down conductors in gutters of a wooden house.
Ground electrode system
The ground electrode system is an element of external lightning protection designed to drain the lightning current into the soil. The grounding of a single-family house is carried out as a closed loop with electrodes made of corrosion-resistant materials. It is laid along the perimeter of the protected building at a depth of 0.5 m and a minimum distance of 1 m from the wall on the side opposite to the house entrance. Do not lay the ground electrode system in the immediate vicinity of passages, porches and the building foundation. This will significantly reduce the risk of electric shock to people.
The grounding electrodes are buried into the soil to a depth of 2-3 meters at an equal distance from each other. They are usually made of stainless and galvanized steel 16 mm in diameter and of copper-bonded steel 14 mm in diameter.
To improve the efficiency of grounding loop by reducing its resistivity, the largest possible contact area of the metallic electrodes surface with the soil is ensured. It is necessary to choose the appropriate dimensions of the grounding electrode system for this purpose.
Grounding for lightning protection shall be arranged in such a way as to protect the building inside the loop. The shape of the loop depends on the shape of the house. According to experts, the more horizontal and vertical electrodes are in the grounding system, the more reliable is the protection. However, experience has proven that three vertical electrodes interconnected with a tape or a round wire are enough for the lightning protection of a wooden house.
All ground loop connections are performed using special clamps, for example, stainless steel clamps, and by socket welding provided that the welded joint is continuous. The connections are thoroughly insulated by a corrosion-resistant tape. Exothermic welding can also be used.
Internal lightning protection of wooden buildings
Many single-family house owners mistakenly believe that the external lightning protection system will ensure the full security of electrical systems inside the building. Meanwhile, powerful electromagnetic pulses of the lightning cause a voltage surge in the house wiring, resulting in damage to electrical devices. The lightning does not necessarily have to strike into the building itself; the electromagnetic field extends to large distances from the lightning strike location. Excessive supply voltage can occur during the spread of charge intercepted by the air terminal system.
In recent years, the demand for internal lightning protection of power grids has increased dramatically due to the fact that the number of electronic devices and household appliances, in particular, microprocessor devices, is steadily growing.
The arrangement of internal lightning protection system requires qualified specialists to make a design for a particular facility and then to install the system.
According to the existing technical regulations, internal lightning protection should be carried out using special devices and consists of the following components:
- equipotential bonding bus that connects all extended metal structures of the house in a single loop with the use of protective conductors. The equipotential bonding system (EBS) eliminates the potential difference between conductive elements and building structures, as well as the related engineering networks and communications between each other and the ground electrode system, thereby protecting the wiring and all connected appliances from the surge.
- Surge protection device (SPD) is a special device designed to limit the effect of electromagnetic pulses and to prevent sparks inside the protected facility. SPDs are mounted on the sections of mains where current leakage can lead to the most dangerous consequences.
It was not until fairly recently that engineers began using SPDs in the electric circuits of single-family houses. The concept of a zone surge protection is used: an SPD of a certain class is set at each section of the circuit.
Depending on their sensitivity to surge, SPD's are grouped into several classes:
class B or class 1 SPDs are used for the protection of electric mains against a direct lightning strike. Such SPDs are installed at the inlet of the electric switchboard. Class C (Class 2) SPDs protect against induced currents. If a very sensitive equipment is present in the house, it is advisable to use class D (Class 3) SPDs.
To make the internal lightning protection of a wooden house effective, it is recommended to use all three classes of SPDs by alternately installing one class after another, or to use a combination of SPDs combining all three classes in one device. The prerequisite is the correct execution of works to equalize the potentials of the facility and the high-quality installation of the grounding device.
Conclusion
The lightning protection of wooden building is a complex of technical solutions implemented to ensure the safety of buildings and related systems, as well as the safety of people and animals in the case of a direct lightning strike or exposure to electromagnetic radiation.
The design of a lightning protection system is made for each facility individually depending on the design features of the built and environment in its location. For example, various types of soil have different current conductivity and resistance, which should be taken into consideration when designing a grounding system.
Calculations of lightning protection are the process of correct designation of security zones above and inside the building, where the spreading of the lightning current after its direct strike into the air terminal should be reliably and safely diverted into the ground.
A wooden house requires a high-quality lightning protection system. When arranging it, it is necessary to focus primarily on the combustion properties of construction materials and fire safety. This is particularly true for houses that rise above other buildings.
The external lightning protection system takes a lightning strike upon itself and drains its current to the soil thereby protecting the building from thermal and dynamic damage.
Equipping the wooden house with special devices for internal lightning protection of electrical mains ensures the safety of the connected electrical appliances, as well as protects users against electric shock.
The state of an installed lightning protection system needs to be regularly inspected for the presence of corrosion and scale on the lightning rod and for the reliability of its fixtures. Every twelve years the ground loop is opened and the condition of electrodes is checked. In case if corrosion is present on more than 1/3 of the ground electrode, the electrode needs to be replaced. Every three years, the connections of lightning protection elements are checked for integrity, contacts are cleaned, and the weakened connections are tightened or replaced.
See also:
- Grounding. What is it and how to make it.
- Lightning protection in a single-family house: standards calculations, examples
- What is Disspation Array Device and how it works?
- Useful materials for designers: articles, recommendations, examples
- Soil resistivity table
Related Articles:
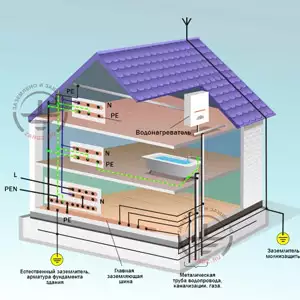
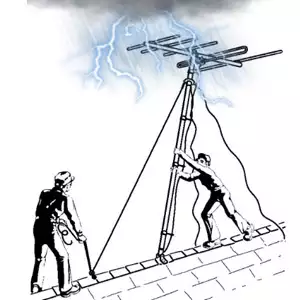
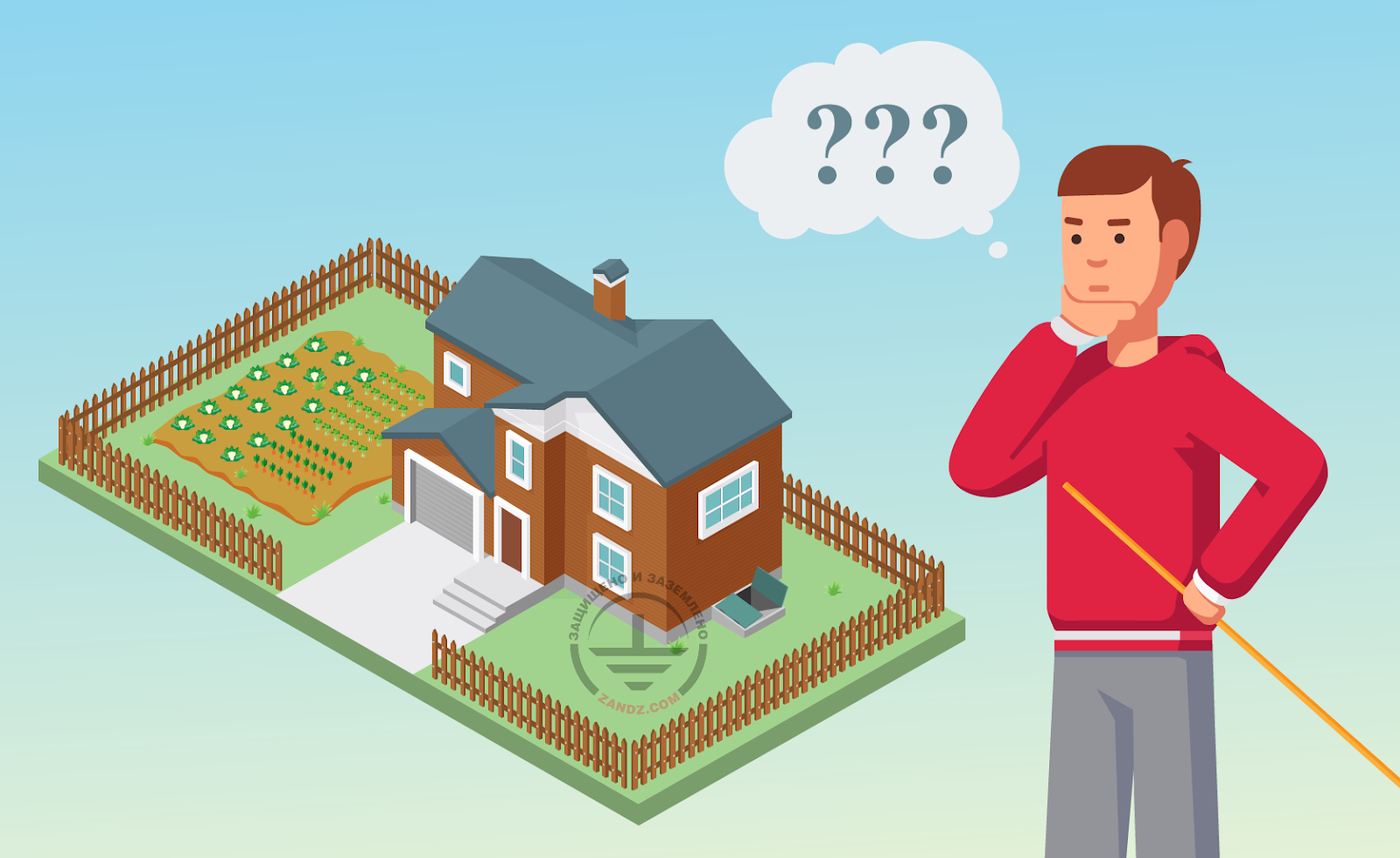
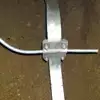
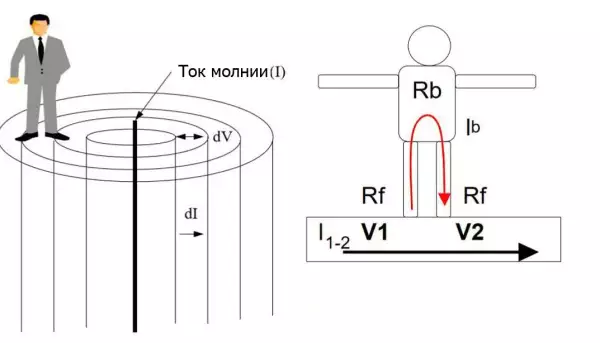
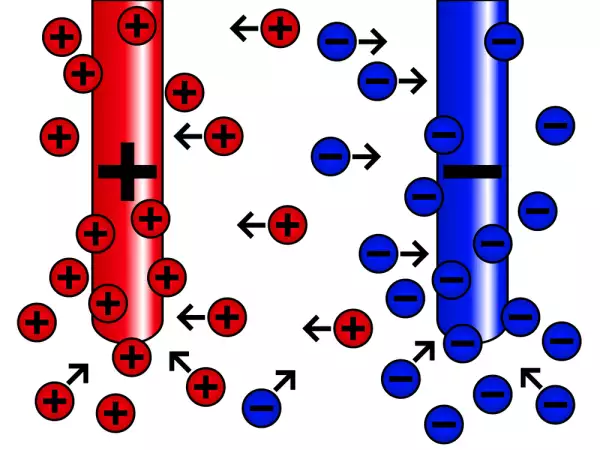
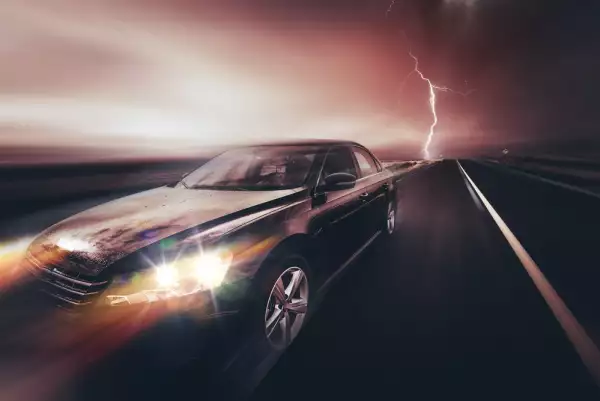
