The forth part of the article "Lightning protection of aircrafts"
One, imagining a graceful construction of a modern airplane fuselage with a thin dural or titan cover, thinks about the thermal impact of powerful lightning strikes. In fact, their real danger is not that great. On fig. 7 the picture of a steel tip of a flagstaff from the Ostankino TV-tower with the traces of multiple lightning strikes. The size of the image is maximally close to the real one.
fig. 7. The picture of the steel tip with the traces of meltback from contact with lightning
The sizes of the cavity are not that impressive. Their depth is close to 1 mm, diameter not more than 10 mm. Lightning won't do anything principally greater to the aluminium surface. The reason is that almost all energy of the lightning flash is dispersed along its channel several kilometers long. A very small share gets into the metal, this share is originated in the thin near-electrode layer with the voltage 10-12 V. Multiply this value to the charge of the lightning flash (maximum 300 Cl), you will get energy spent on the heating and melting of the fuselage, about ∆We = 3000 J. At the specific heat of aluminium for the studied range of temperature cAl ≈ 800 J (kg, degree), temperature of melting TAl ≈ 660oC and specific fusion heat λAl ≈ 3,9×105 J/kg the mass of the melted material of the fuselage, estimated as
(5)
will be a bit more than 3 r. In real conditions even less. The thing is that during a flight, the point of the lightning channel contact moves on the fuselage metal, making characteristic jumps with the interval of several cantimeters. The effect is more noticeable, the higher is the flying speed. In the result, the energy is produced not in one but in several places, and that is why the fusion penetration seat decreases in sizes.
In the part of mechanical impacts of lightning, the greater dangers is demonstrated by the contact of its channel with the dielectric fuselage of the nose spinner, covering the course poisitioner and other antenna systems, and also the transparency of the cockpit. If not to take special measures, an electric puncture of the dielectric is possible. It is impossible to substitute it by metal according to the condition of radio-transparency (necessary for a positioner) and optical transparency (necessary for pilots). It is necessary to place thin metal lightning rod buses connected with the fuselage on the spinner. But they cloud the sight of the positioner. In order to reduce the blanketing, the buses are formed of small metal fragments not connected with each other. At the development of the leader from these buses, the isolation intervals are overlapped by plasma channels and work as a single lightning rod conductor, draining the lightning current to the fuselage.
Finally, it is necessary to remind about the shock wave from the lightning channel. Its temperature raises up to 30 000 C in approximately 10 ms. IndIn fact, the process has a character of an explosion. An onground observer is only a bit worried by the thunder claps. But a supersonic wave, entering the air intake of the engine, can bring to fatal consequences. Sweeping the combustion products, it stops the turbine. There is a special term for that- engine surge. It is not applied on passenger airplanes, because lightning cannot get to the pilons of wings, where engines are now mounted.
E. M. Bazelyan, DEA, professor
Energy Institute named after G.M. Krzyzanowski, Moscow
Read more "5. Airplane electrization charge"
See also:
- Useful materials for grounding and lightning protection designers
- Free webinars with the leading industry experts
- Real-life examples of grounding and lightning protection calculations
Related Articles:
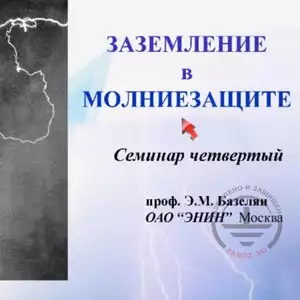
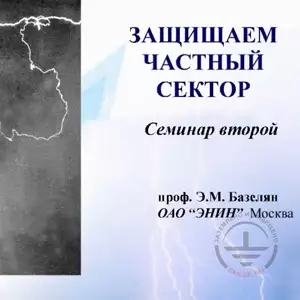
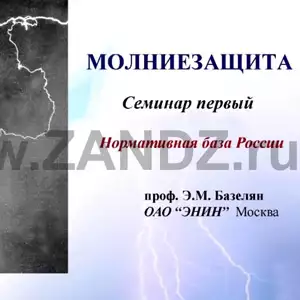
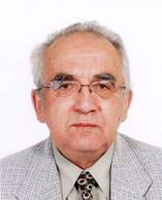
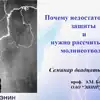
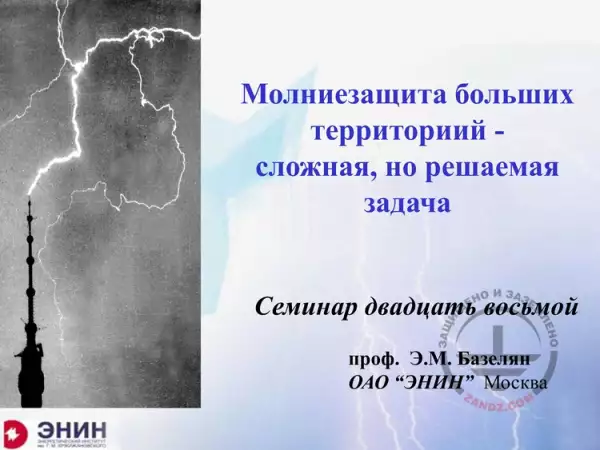
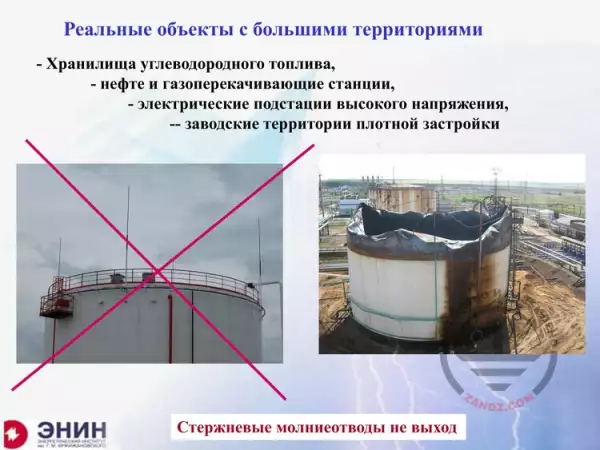
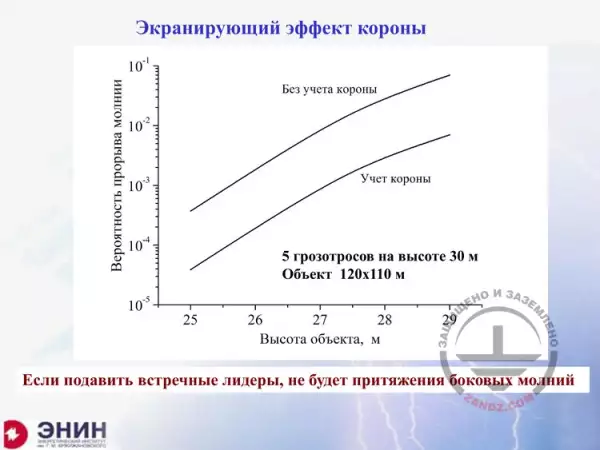