Grounding is a purposeful electrical connection of an element of electricity - generating equipment or equipment with ground electrode system. Grounding device presents itself a series of conductive elements that are in contact with the zero ground potential. Groud electordes are used in order to ensure safe and efficient operation of electricity-generating equipment, as well as for lightning protection. When selecting the materials of the ground electrode, electrical resistance of the conductor (the lower the resistance is , the more efficient is the device), reasonable price and sufficient durability are important parameters. That is, conductive properties of a grounding devices must ensure safe operation of equipment throughout its lifetime. This means that the material must possess not only good conductivity, but also be corrosion resistant.
GOST R 50571.5.54-2013 / IEC 60364-5-54: 2011, paragraph 542.2.1 stipulates that types, materials and dimensions of ground electrodes should provide corrosion and mechanical resistance for lifetime. Table 5.54 of GOST lists the minimum dimensions of eletrodes made of most widespread corrosion resistant materials. Despite its high mechanical resistance, black steel is often subject to destruction in soil (up to 7 years). In the process of interaction with the aggressive environment, this material acquires non-uniform structure and increases in volume. Fluffy shell is formed on the steel surface, which significantly reduces contact of the element with the soil. As a result, resistance to current spreading increases. In this regard, the use of ferrous metals is inadmissible.
To date, copper wires, stainless steel materials, or conductive corrosion-resistant coatings applied to the black steel are used to avoid the destruction of the ground electrode . The latter option is cheaper and highly effective, because an alternating electrical current spreads mainly on the conductor's surface. Applying of a layer with a greater conductivity to the surface of ferrous metal reduces resistance to current spreading all over the conductor. For example, zinc or copper coating of ferrous metal may increase conductive properties of the steel grounding device up to 6 times.
Let's consider basic advantages and disadvantages of these materials.
Stainless steel elements of grounding systems: rod, tape, wire
Stainless steel is a material that is resistant to interaction with the environment (corrosion resistant). These properties are due to the presence of chromium in the steel. Thus its content should be not less than 12.5%, then the potential of steel becomes positive and that prevents corrosion. Besides that, chromium, being oxidized forms passive layer of chromium oxide (Cr2O3) on the steel surface. To increase anticorrosive properties , steels is alloyed with nickel, molybdenum, nitrogen. Also, these materials have high strength values. The service life of "stainless steel" can reach 100 years.
Galvanized steel elements of grounding systems: rod, tape, wire
The use of galvanized steel which is a cheaper material than "stainless steel" became popular. Zinc has quite a low resistivity ( 0,059 ohm ∙mm2/m). Zinc coating is applied to ferrous metal by hot galvanizing, its thickness is 0.080 mm.
In a pair of zinc-steel , zinc is more electrochemically active material, therefore, it begins to destroy earlier than the steel base. At the insertion of a galvanized ground electrode to a hostile environment (in particular - soil), zinc will gradually dissolve, protecting black steel against corrosion. And even deep scratches, formation of which is possible at the electrode surface during mounting, can not lead to rapid emergence of corrosion. While zinc layer remains around the site of damage, corrosion will not spread. Natural process of zinc oxidation is very lengthy. Galvanized ground electrodes are applied in acidic and neutral environments. The service life of the product may be more than 30 years.
Copper elements of grounding systems: rod, tape, wire
Copper - non-ferrous metal, the main distinctive characteristics of which are high electrical conductivity, ductility, corrosion resistance, good machinability. This metal has a very low resistivity. It is only 0.0175 ohm ∙ mm2/m. The only drawback of copper is its relatively high price and low strength compared to steel. Full copper rods bend quite easily when inserting them in the ground. To avoid these problems and increase lifetime of the finished product, copper is used as a highly conductive coating.
The copper coating is applied to black steel by electrochemical method. The essence of electrochemical copper plating of steel is as follows: a steel rod (cathode) is connected to the negative terminal of the current source, and copper plates (anode) - to the positive. Electrodes are placed in an electrolyte solution containing copper salt. Under the influence of an electric current, positively charged copper ions Cu2+ move to the anode (the steel base of the ground electrode) and subside on its surface in the form of pure metal. The resulting material is called copper-plated steel.
Copper-bonded coating is characterized by high adhesion to different metals, high ductility and conductivity. Besides, copper plated steel has a higher strength than copper.
Adhesion of copper to steel is higher than that of zinc, therefore, even under considerable mechanical stress , there is no copper peeling from the base. The thickness of copper coating is typically 0.250 mm.
Copper plated ground electrode has several advantages compared to the galvanized. The fact is that copper is less electrochemically active (it's obvious if to look at metal galvanic series) material than steel and zinc. Therefore, in a pair of copper-steel, steel will be destroyed quicker, and until all of it is destroyed the copper coating remains intact. At a sufficient thickness, copper coating lasts longer than the galvanized, being more efficient and corrosion resistant.
Copper-bonded steel is widely used in practice, as a material for manufacture of ground electrodes. Copper coated steel rods can be applied in any conditions. The service life of copper-bonded steel as a grounding element exceeds 35 years.
See also:
- Grounding systems. Recommendations of European standards
- Copper-bonded steel test
- Grounding. What is it and how to make it.
- Types of air terminals: mast, cable wire and mesh cage
- Surge protection
Related Articles:

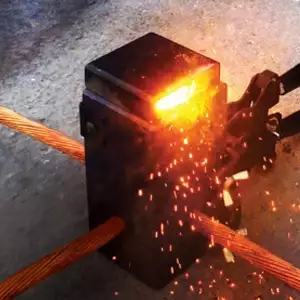
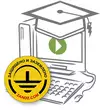
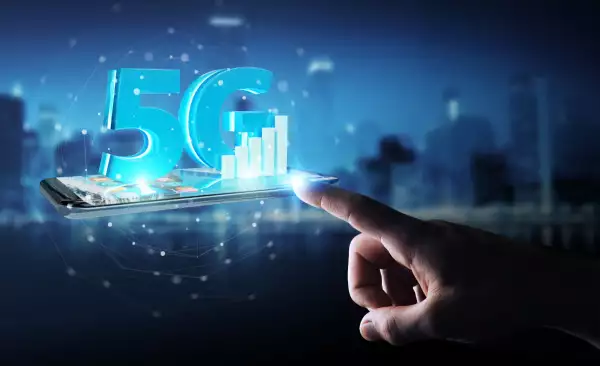
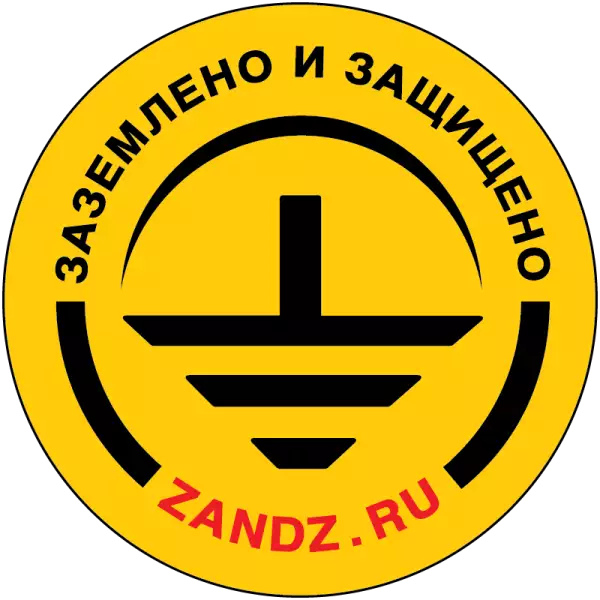